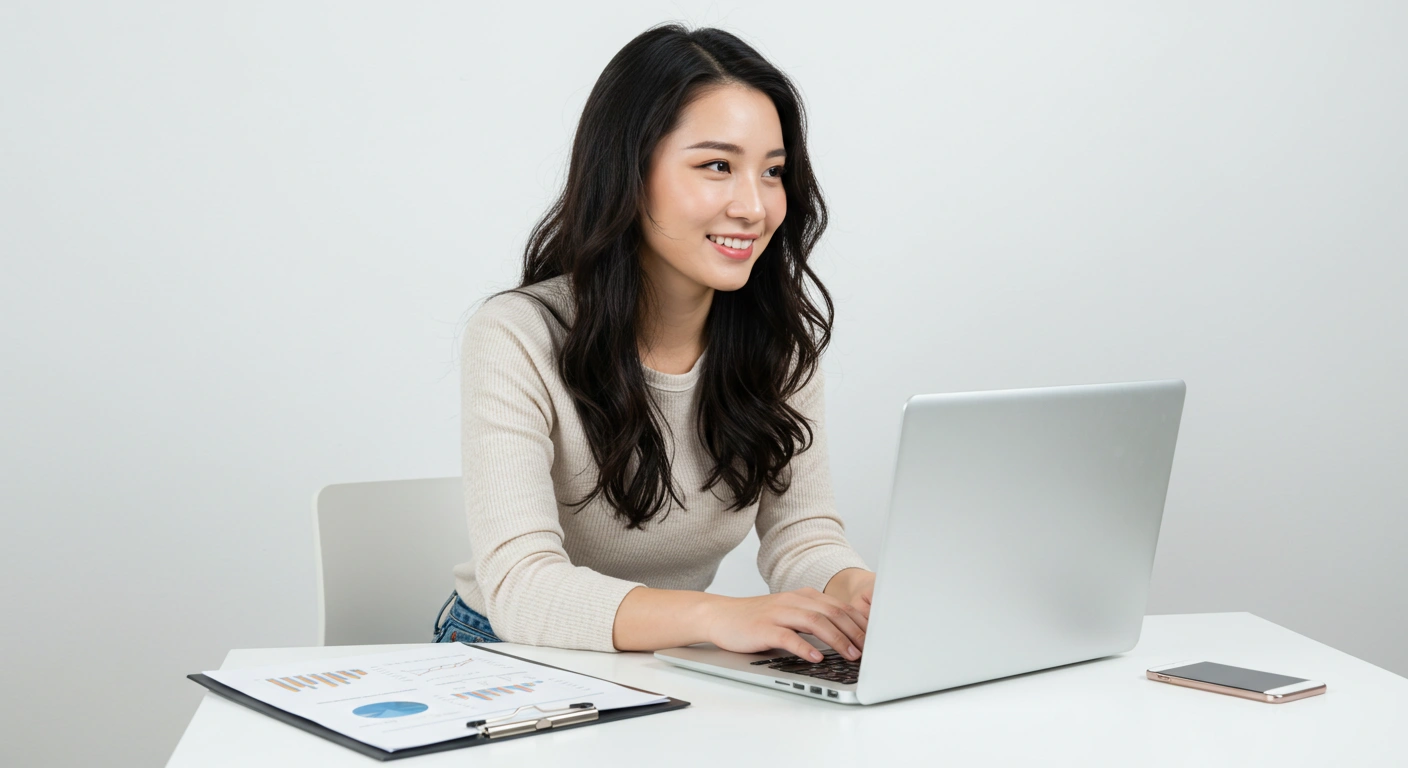
Japanese 5s Tactic
The Japanese 5s tactic was first introduced by Toyota to eliminate unnecessary waste and inefficiency, and is an approach that allows for effective results in workplace organization. This approach, which was initially designed to be applied in production, has found its place in the education curriculum in Japan today, as it has been understood that it can also be applied to the lives of individuals.
What is the Japanese 5S Tactic and How is it Applied?
The Japanese 5s tactic is named after the first letters of the words Seiri, Seiton, Seiso, Seiketsu, Shitsuke and has passed into our language as sorting, order, cleanliness, standardization and discipline. It was designed to cover a series of methodologies such as JIT (just in time) and JIDOKA to reduce waste and increase efficiency in post-Japanese production.
Initially implemented only by the creators of the tactic and kept secret, the approach began to be implemented by foreign companies after the economic boom in Japan in the 1980s.
So what are the steps that make up this tactic? Let's go into a little detail.
Sorting: Gather only the materials needed for production. This way, you can understand what is needed and what is not needed for production and remove what is not needed from the production area.
Organization: Make sure all items are organized and each item has a designated place. Arrange all items left in the workplace in a logical manner to make it easier for employees to complete their tasks. This often requires a number of measures, such as placing items in ergonomic positions where people do not have to bend over or make extra movements to reach them.
Cleanliness: The sum of proactive efforts to keep workplace areas clean and tidy to ensure purposeful work. This means cleaning and maintaining the newly organized work area. It also includes routine tasks such as mopping, dusting, or maintaining machinery, tools, and other equipment.
Standardize: Create a set of standards for both the organization of the organization and the processes that are performed. In essence, this is where you take the first three S’s and set the rules for how and when these tasks are to be performed. These standards may also include a set of mnemonic devices such as charts, lists, and plans.
Discipline: Discipline, the last link in the Japanese 5s tactic, is not only a part of the approach but also a concept of life. Continuing the new practices you have presented so far with discipline also allows new members of the organization to adapt to this situation quickly.
Benefits of 5S System
The Japanese 5s tactic has become an indispensable part of the lean production method. This approach not only contributes to the establishment of high standards in the workplace, but also supports the creativity of employees. In a workplace, employees working in a lean, well-maintained, standardized, sustainable and disciplined structure, first of all, contributes to the motivation of employees and their enjoyment while working.
Although implementing the Japanese 5s tactic can be a difficult process for an organization in some cases, the best part about this tactic is that you can break it down into pieces and apply them one by one over time. For example; if you are not in a time frame that suits your attempt to reduce materials used in production, you can continue to implement it without interrupting the process by moving on to the next step.
The Japanese 5s tactic is an approach designed to bring order and efficiency to your business by nature. Unlike the days when the approach emerged, today it is possible to adapt computer technologies to the process. Please contact us to get detailed information on how to integrate the powerful infrastructure brought by technology into all the processes you implement in your business.